Articles
ESCadrille 3.0 : une nouvelle ère
ESCadrille 3.0 : une nouvelle ère 19 août 2019 : une date clé pour ESCadrille. Ce jour-là, notre Junior-Entreprise a franchi une étape majeure : le rebranding complet de notre identité visuelle ainsi que la refonte intégrale de notre site Internet. À travers cet...
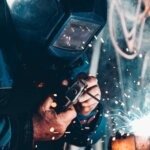
Où en est l’industrie française ?
L'industrie française, une longue histoire d'amour n'est-ce pas ? Entre la gloire et les tumultes de son existence, cette industrie s'est fortement transformée au cours des années. Toutefois, ce n'est pas une problématique simple puisque ce sujet est au centre des débats politiques depuis...
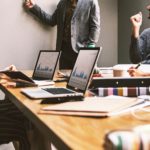
Focus sur l’entrepreneuriat
Connaissez vous "LE" chiffre de l'entrepreneuriat ? 4 entrepreneurs sur 10 étaient salariés avant de créer une entreprise. Audrey Baillot, Sylvain Juliachs (Insee) L'année 2022 fut prolifique pour la création d'entreprise. En effet, encore une année où les entrepreneurs ont été...
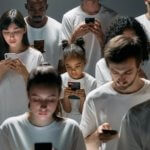
Génération Z : Le défi (et l’opportunité) des marques aujourd’hui
Une génération qui redéfinit les règles du jeu La génération Z – ces jeunes nés entre 1997 et 2010 – ne cesse d’intriguer, de questionner et de bousculer les codes traditionnels du marketing. En tant que digital natives, ils n’ont jamais connu un monde sans Internet, sans...
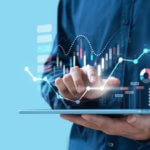
Comment une Junior Entreprise peut booster la stratégie digitale des PME en 2025
La transformation digitale En 2025, la transformation digitale n’est plus une option pour les PME : c’est un levier de croissance, de compétitivité et de visibilité. Mais face à la complexité des outils numériques, à l’évolution des tendances et à la rapidité des...
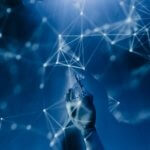
L’intelligence artificielle : introduction, principes et exemples concrets
L’intelligence artificielle : introduction, principes et exemples concrets Cette introduction à l’IA vous propose de découvrir les fondements de l’intelligence artificielle, ses principes clés et ses applications concrètes dans notre quotidien professionnel et...
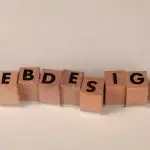
Pourquoi la communication est plus stratégique que jamais en 2025
En 2025, les entreprises ne peuvent plus se permettre de négliger leur communication. Dans un contexte saturé de contenus, où chaque marque rivalise d'attention, une stratégie de communication efficace n’est plus un luxe : c’est une nécessité. Une ère de l'attention...
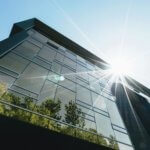
Stratégie ESG entreprise 2025 : 3 leviers pour se démarquer
Stratégie ESG entreprise 2025 : 3 leviers pour se démarquer Vous vous demandez pourquoi vos concurrents sont plus visibles sur certains marchés ? Pourquoi leurs projets remportent davantage d’appels d’offres ou attirent plus facilement des partenaires ? Ces écarts de performance...